Reducing waste
We must reduce, re-use and recycle the materials we use to avoid waste.
We have a big opportunity to support a more circular economy. That means using fewer natural resources, keeping materials in use for longer, and cutting waste to a minimum. This will also help us significantly reduce our carbon emissions.
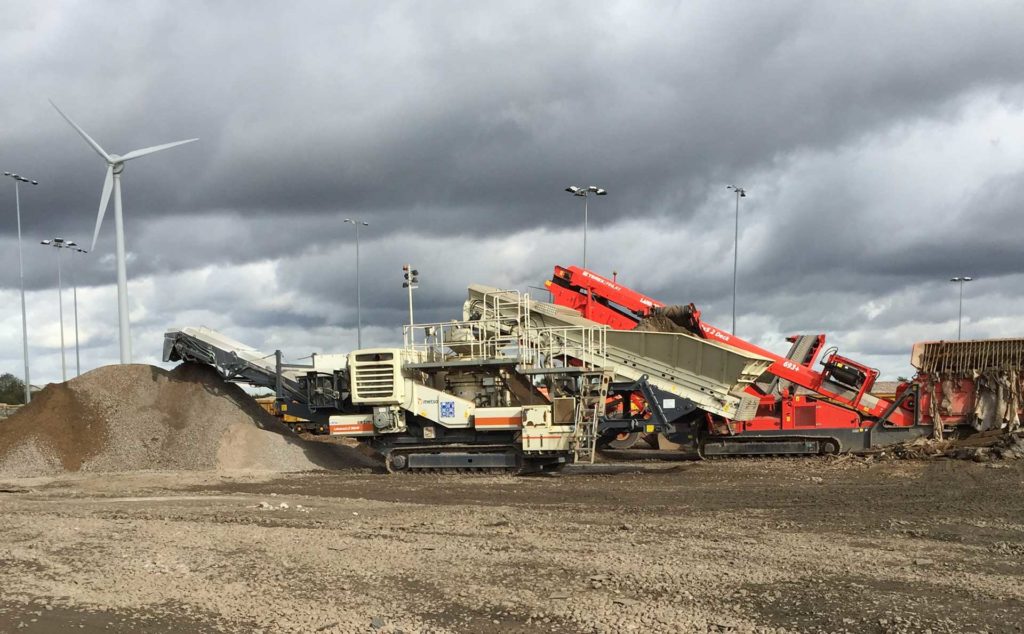
Our ambition for minimal waste
We spend around £7bn a year through our supply chain. That’s because building and maintaining the railway takes a huge amount of materials. Our activities produce a lot of waste; 2.1 million tonnes in 2018/2019. We must use less and manage unavoidable waste better.
In our Environmental Sustainability Strategy we’ve committed to reuse, repurpose or redeploy all surplus resources and embed circular economy thinking into the rail industry by 2035. To achieve this, we need to bring the whole industry along with us.
We will be setting high standards for our supply chain. We will work closely with our suppliers, for example, to research and develop new, innovative secondary materials that reduce our reliance on new materials and discover new ways of designing and building assets to keep materials and resources in use for longer.
What are we doing to reduce our waste?
We want to form meaningful partnerships across the rail industry and infrastructure sector to share resources, waste streams, and best practice. Our work on sustainable use of materials supports our other priorities. Thinking about the ‘whole life’ of assets and products helps to reduce carbon, minimise waste and use of materials and be more resilient to climate change in the long term.
Key milestones
- 2021 – Identify and prioritise materials and waste within our supply chain.
- 2022 – Implement a circular economy policy that aims to recycle materials and reduce waste.
- 2023 – Adopt standards that include reusing and recycling materials.
- 2024 – Embed reusing and recycling tools into the procurement process. Adopt standards that include reusing and recycling materials.
- 2029 – Reuse and recycle everything.
Over the last ten years, the system recovered 2.6 million tonnes of track ballast for reuse back onto the track, saving Network Rail £9 million in material costs. Where the used track ballast no longer meets product quality, the rejected ballast is transported by rail to one of Network Rail’s nine aggregate handling depots (AHDs). The AHDs process the used ballast material alongside redundant railway sleepers and rail from maintenance and capital delivery projects to provide reuse opportunities – either back into the railway, in land reclamation, or sold on for reuse in heritage railways or construction.
This approach’s benefit is that waste is moved up the waste hierarchy wherever possible. We can invest the financial returns from selling the redundant materials back into the railway.